Open Cathode vs. Closed Cathode Fuel Cells
Open vs. closed cathode fuel cells: Which is better? Explore their cooling, efficiency & role in clean energy.
FUEL CELL
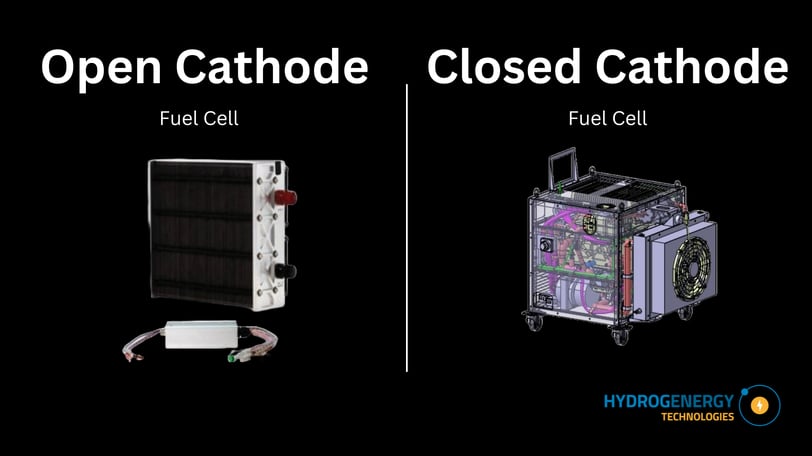

Fuel cells are a cornerstone of the clean energy transition, offering high efficiency and zero emissions for a range of applications, from electric vehicles to stationary power generation. Among the various types of fuel cells, proton exchange membrane fuel cells (PEMFCs) are particularly popular due to their fast start-up, high power density, and scalability.
Within PEMFCs, there are two primary configurations: open cathode and closed cathode fuel cells. Each system has distinct advantages and challenges, impacting its performance, cooling mechanism, and efficiency. This article provides a comprehensive technical analysis of these two fuel cell types, addressing key questions regarding their operation, cooling strategies, and potential improvements, including the use of a dedicated oxygen line at the cathode.
1. Understanding Open Cathode and Closed Cathode Fuel Cells
Open Cathode Fuel Cells
Open cathode fuel cells use ambient air for both oxygen supply and cooling. They rely on a forced airflow system that provides oxygen to the cathode while simultaneously dissipating heat generated during the electrochemical reaction.
馃敼 Operating Principle:
Air is drawn into the cathode compartment, where oxygen participates in the redox reaction.
The same airflow removes excess heat and carries away byproducts like water vapor.
No separate cooling system is needed, simplifying the design and reducing costs.
Closed Cathode Fuel Cells
Closed cathode fuel cells, in contrast, operate with a controlled oxygen supply and typically employ a dedicated cooling system. These cells can be air-cooled or liquid-cooled, depending on power requirements and operational constraints.
馃敼 Operating Principle:
Oxygen (either from ambient air or a separate oxygen source) is supplied through a controlled inlet.
Excess heat is managed via an independent cooling system, which may be air- or liquid-based.
Water management is actively regulated to prevent membrane flooding or drying.
2. Can Closed Cathode Fuel Cells Be Air-Cooled?
Yes, closed cathode fuel cells can be air-cooled, but this approach has limitations compared to liquid cooling.
馃敼 Air-Cooled Closed Cathode Fuel Cells:
Use fans or heat sinks to remove excess heat.
Suitable for moderate power applications, such as stationary backup power.
Efficiency is lower compared to liquid cooling, as air has a lower heat capacity.
馃敼 Liquid-Cooled Closed Cathode Fuel Cells:
Use coolant circulation (water, glycol) for heat dissipation.
Provide higher efficiency and power density, making them ideal for high-demand applications like heavy-duty vehicles and industrial power systems.
Require additional complexity in terms of pumps, radiators, and heat exchangers.
Conclusion: While air cooling is feasible for closed cathode fuel cells in lower-power applications, liquid cooling is preferred for higher-power, high-efficiency systems due to superior thermal regulation.
3. What Happens If a Separate Oxygen Line is Used at the Cathode?
Providing a dedicated oxygen line to the cathode instead of relying on ambient air can significantly impact fuel cell performance and efficiency.
Advantages of a Separate Oxygen Line:
路 Increased Reaction Efficiency: A dedicated oxygen supply eliminates nitrogen and other air components, improving reaction kinetics at the cathode.
路 Lower Parasitic Losses: Without the need for large air blowers, energy consumption decreases, improving overall efficiency.
路 Better Water Management: Since nitrogen is absent, water vapor behavior becomes more predictable, reducing risks of membrane flooding or drying.
路 Improved Thermal Control: Separating oxygen supply from cooling airflow allows better independent regulation of temperature and reaction rates.
Challenges:
路 Additional Infrastructure: Requires dedicated oxygen storage or on-site oxygen generation.
路 Cost Implications: Pure oxygen supply is more expensive than using ambient air.
路 Safety Concerns: Handling pure oxygen introduces risks of combustion in case of leaks.
Conclusion: A separate oxygen line can significantly boost efficiency, power density, and system stability, making it an ideal choice for high-performance fuel cells in aerospace, industrial, and high-power applications.
4. Key Technical Comparisons: Open Cathode vs. Closed Cathode Fuel Cells
5. Application Suitability: Which Fuel Cell Type is Best?
Best Uses for Open Cathode Fuel Cells
Small drones and UAVs
Portable power generators
Lightweight electric vehicles (e-bikes, scooters)
Low-power industrial applications
Best Uses for Closed Cathode Fuel Cells
Heavy-duty transport (trucks, buses, trains)
Backup power for telecom/data centers
Marine and aerospace applications
Large-scale stationary power generation
6. Key Takeaways
Both open cathode and closed cathode fuel cells have their strengths and weaknesses, making them suitable for different applications. Open cathode fuel cells are simpler, cost-effective, and ideal for portable or low-power systems. Meanwhile, closed cathode fuel cells offer superior efficiency, higher power output, and better environmental control, making them suitable for high-demand applications.
Additionally, implementing a separate oxygen supply at the cathode can further enhance performance, particularly in high-efficiency applications such as aerospace and industrial power systems. While this approach adds complexity and cost, it provides better efficiency, water management, and power density.
Final Takeaway: The choice between open and closed cathode fuel cells鈥攁nd whether to use a separate oxygen line鈥攄epends on the power requirements, cost considerations, and application needs. As fuel cell technology advances, these configurations will continue to evolve, optimizing energy efficiency and sustainability for a cleaner future.