What is a Solid Oxide Electrolyzer ?
What is Solid Oxide Electrolyzer | Green Hydrogen | SOEC vs PEMEC | SOEC Advantages | Sizing of SOEC | Challenges and Considerations
ELECTROLYZER
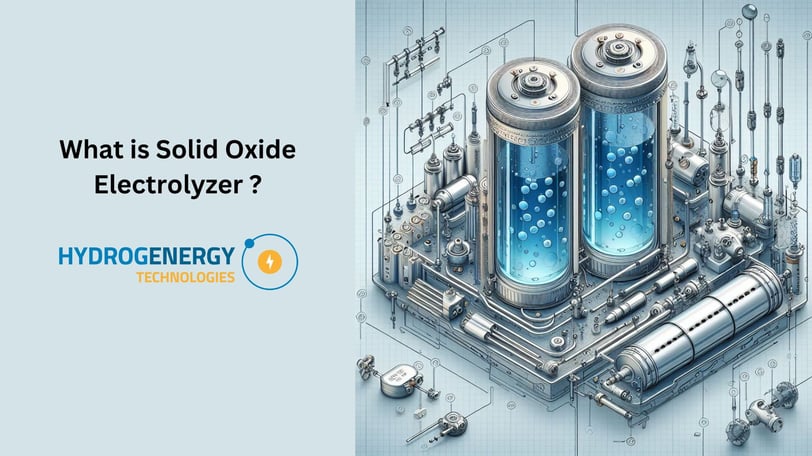
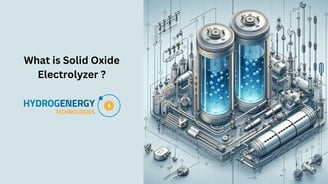
Solid Oxide Electrolyzers: Unveiling the High-Temperature Powerhouses for Green Hydrogen Production
The clean energy revolution hinges on finding sustainable ways to produce versatile fuels like hydrogen. Solid oxide electrolyzers (SOECs) have emerged as a promising solution, offering a high-temperature approach to generating green hydrogen. This comprehensive blog dives into the intricate workings of SOECs, explores their role in green hydrogen creation, and compares them to other popular electrolyzer technologies. By understanding the technicalities and advantages of SOECs, we can appreciate their potential in revolutionizing hydrogen production.
Inside the SOEC: A High-Temperature Wonderland
SOECs stand out from other electrolyzer technologies primarily due to their high operating temperatures and use of solid ceramic materials as the electrolyte. Let's break down the key components that make an SOEC tick:
Anode: This porous electrode, typically constructed from nickel-yttria stabilized zirconia (Ni-YSZ), facilitates the passage of oxygen ions (O2-) while acting as a barrier for electrons. The Ni-YSZ anode is robust and capable of withstanding the harsh high-temperature environment within the SOEC.
Cathode: Made from materials such as strontium-doped lanthanum manganite (LSM), the cathode allows oxygen ions to pass through while blocking electrons. LSM is chosen for its excellent conductivity and stability at high temperatures.
Electrolyte: The heart of the SOEC is the dense ceramic membrane, usually yttrium-stabilized zirconia (YSZ). This specialized material enables oxygen ions to travel through it under the applied electrical field but acts as an insulator for electrons.
The Magic of High Temperatures
SOECs operate at significantly higher temperatures (700-1000°C) compared to proton exchange membrane (PEM) electrolyzers, which typically operate at 50-80°C. This seemingly simple difference unlocks several advantages:
Enhanced Efficiency: High temperatures lead to increased thermal energy, which can supplement the electrical energy required for the electrolysis process. This thermal assistance potentially results in higher overall efficiencies compared to PEM technology. SOEC efficiencies can reach up to 90%, compared to around 60-70% for PEM electrolyzers.
Material Flexibility: The high-temperature environment within SOECs allows for more flexibility in material selection. This is particularly beneficial for the anode, where materials like Ni-YSZ can withstand harsh conditions and facilitate the hydrogen formation reaction efficiently.
Fuel Source Versatility: Unlike PEM electrolyzers that require ultra-pure water feedstock, SOECs can tolerate some impurities. This makes them suitable for utilizing hydrogen derived from biomass gasification, which may contain trace amounts of carbon monoxide (CO).
From Electricity to Green Hydrogen: The SOEC Process
Understanding the detailed electrochemical process within an SOEC provides insight into how green hydrogen is produced:
Electrical Input: An external DC power source provides the electrical energy needed to drive the electrolysis process. Ideally, this electricity comes from renewable sources like solar or wind, making the produced hydrogen truly "green."
Electrolysis at High Temperature: When an electrical field is applied, water molecules (H2O) near the cathode are split into hydrogen ions (H+) and oxygen ions (O2-).
Oxygen Ion Migration: Due to the high temperature, the oxygen ions become highly mobile within the YSZ electrolyte. These oxygen ions travel through the electrolyte from the cathode towards the anode.
Hydrogen Formation: At the anode, the migrated oxygen ions react with electrons readily available due to the anode material's properties. This reaction produces water vapor (H2O) and releases pure hydrogen gas (H2) into the collection chamber.
The Green Hydrogen Advantage
Since the electricity used in this process can come from renewable sources, the resulting hydrogen is considered "green hydrogen" with minimal environmental impact. This green hydrogen can then be utilized in various applications like clean fuel cell vehicles or for industrial processes requiring a clean, high-energy fuel source.
SOEC vs. PEM: A Tale of Two Electrolyzer Technologies
While both SOECs and PEM electrolyzers are used for hydrogen production, they have distinct characteristics that make them suitable for different scenarios. Let's compare these technologies in detail:
Efficiency Powerhouse
SOECs: Hold the potential for higher efficiencies due to their ability to utilize waste heat from high-temperature operations. This can significantly reduce the overall electrical energy input required for hydrogen production. SOEC efficiencies can reach up to 90%, whereas PEM electrolyzers typically range from 60-70%.
PEM Electrolyzers: While less efficient, PEM electrolyzers operate at lower temperatures (50-80°C), which allows for quicker start-up times and better compatibility with intermittent renewable energy sources.
Fuel Source Flexibility
SOECs: Can handle impurities in the hydrogen feedstock, making them more versatile in terms of the types of water sources they can use. This includes using water with higher levels of impurities or hydrogen derived from biomass gasification.
PEM Electrolyzers: Require ultra-pure water to prevent degradation of the membrane, which can be a limitation in certain applications.
Size and Scalability
SOECs: Generally more suitable for large-scale industrial applications due to their higher efficiency and ability to operate continuously at high temperatures. Large-scale SOEC plants can produce hydrogen at lower costs per unit of energy.
PEM Electrolyzers: More adaptable to smaller, decentralized systems due to their lower operating temperature and quick response to changes in power supply, making them ideal for integration with renewable energy sources like solar and wind.
Operational Durability
SOECs: The solid ceramic materials used in SOECs are highly durable and can withstand the high operating temperatures, potentially offering longer operational lifespans compared to the membranes used in PEM electrolyzers.
PEM Electrolyzers: The polymer membranes used in PEM electrolyzers are sensitive to impurities and require frequent maintenance to ensure longevity, which can increase operational costs over time.
Cost Considerations
SOECs: The initial cost of SOECs can be higher due to the materials and technology involved. However, their higher efficiency and longer lifespan can lead to lower overall costs in large-scale, continuous operations.
PEM Electrolyzers: Generally have lower upfront costs and are more commercially available. Their simpler construction and lower operating temperatures contribute to reduced initial expenses, but operational costs may be higher due to maintenance needs.
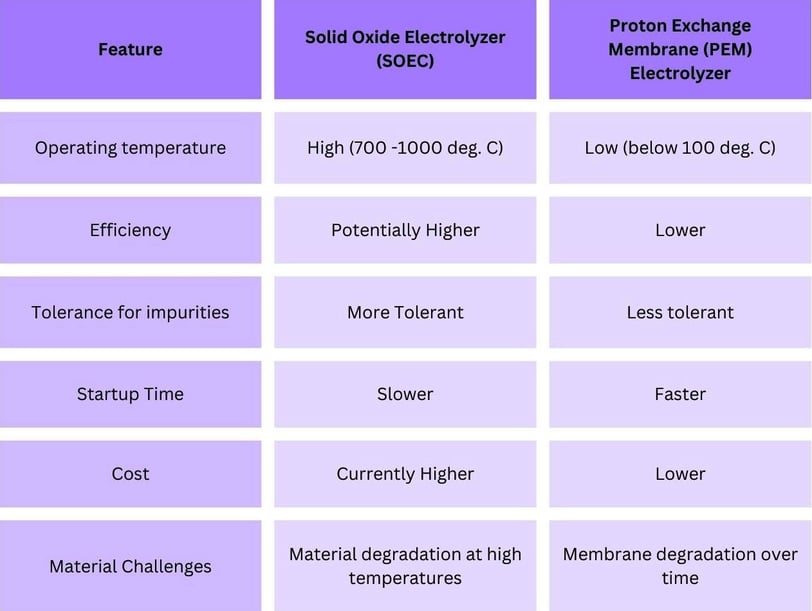
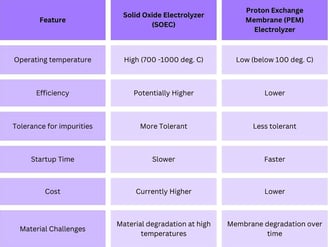
General Advantages Over Other Technologies
SOECs offer several advantages over other hydrogen production technologies, making them a strong candidate for future large-scale hydrogen production:
Lower Energy Costs
The high efficiency of SOECs translates to lower overall energy costs for hydrogen production. By utilizing waste heat and operating at high temperatures, SOECs can achieve impressive energy conversion efficiencies, reducing the amount of electrical energy needed to produce hydrogen.
Thermal Integration
SOECs can integrate with other high-temperature processes, such as industrial furnaces or combined heat and power (CHP) systems, to utilize waste heat effectively. This integration can further enhance the overall efficiency of the hydrogen production process and reduce energy costs.
Reduced CO2 Emissions
By using renewable energy sources and tolerating impurities in feedstocks, SOECs contribute to lower carbon footprints in hydrogen production. This aligns with global efforts to reduce greenhouse gas emissions and transition to sustainable energy systems.
Enhanced Durability
The solid ceramic materials used in SOECs are highly durable and can withstand the high operating temperatures, potentially offering longer operational lifespans compared to the membranes used in PEM electrolyzers. This durability can reduce the frequency of maintenance and replacement, further lowering operational costs.
Sizing of SOEC Plants: Advantages and Considerations
Large-Scale Applications
SOECs are particularly well-suited for large-scale industrial applications due to their high efficiency and ability to operate continuously at high temperatures. Large-scale SOEC plants can produce hydrogen at lower costs per unit of energy, making them economically viable for industries with high hydrogen demands. The scalability of SOECs allows for the development of centralized hydrogen production facilities that can supply hydrogen to multiple end-users, including transportation, power generation, and chemical manufacturing.
Decentralized Systems
While SOECs are often associated with large-scale applications, advances in technology and cost reductions could enable their use in decentralized systems. Smaller SOEC units could be deployed in locations with abundant renewable energy sources, such as solar or wind farms, to produce green hydrogen on-site. This decentralized approach can reduce transportation costs and provide a reliable hydrogen supply for remote or off-grid communities.
Integration with Renewable Energy Sources
SOECs can be integrated with renewable energy sources to produce green hydrogen efficiently. By utilizing excess renewable energy during periods of low demand, SOECs can operate continuously and maximize hydrogen production. This integration can also help stabilize the grid by absorbing excess electricity and converting it into storable hydrogen, which can be used later when energy demand is high.
Challenges and Future Prospects
Technical Challenges
Despite their advantages, SOECs face several technical challenges that need to be addressed to achieve widespread adoption. These challenges include:
Materials Degradation: The high operating temperatures can lead to the degradation of materials over time. Research is ongoing to develop more robust materials that can withstand prolonged exposure to high temperatures and harsh operating conditions.
Cost Reduction: The initial cost of SOECs is higher compared to other electrolyzer technologies. Continued advancements in materials science and manufacturing processes are needed to reduce costs and make SOECs more economically competitive.
System Complexity: The integration of SOECs with other high-temperature processes requires careful system design and optimization. Developing efficient and reliable systems that can operate continuously and handle variations in feedstock quality is crucial for the successful.
View our product page to purchase Fuel Cells, Electrolyzers and other hydrogen related equipments.